[{“box”:0,”content”:”[if 992 equals=”Open Access”]
Open Access
n
[/if 992]n
n
n
n
n
- n t
n
Kousik Kumaar R., Somasundara Vinoth K, Srikanth H.V., Boopathy G
[/foreach]
n
n
n[if 2099 not_equal=”Yes”]n
- [foreach 286] [if 1175 not_equal=””]n t
- Assistant Professor, Assistant Professor, Associate Professor and Head, Assistant Professor, Department of Aeronautical Engineering, NITTE Meenakshi Institute of Technology, Bangalore, Department of Production Engineering, PSG College of Technology, Department of Aeronautical Engineering, NITTE Meenakshi Institute of Technology, Bangalore, Department of Aeronautical Engineering, Vel Tech Rangarajan Dr. Sagunthala R&D Institute of Science and Technology, Chennai,, Karnataka, Tamil Nadu, Karnataka, Karnataka, India, India, India, India
n[/if 1175][/foreach]
[/if 2099][if 2099 equals=”Yes”][/if 2099]nn
Abstract
nThe vital focus of the research is intended in examining the aspect that impact the rate of wear for a hybrid aluminium metal matrix composite. The percentages of two reinforcements that are employed, the weight, and the sliding speed are the variables taken. The procedure entails employing the vortex-stir casting process to produce the hybrid composite. Utilizing a pin-on-disc apparatus, the fabricated composite materials are evaluated in compliance with the ASTM G99 standard. The test settings embrace varying weights and sliding speeds ranging from of 10 N to 30 N and 1 m/s to 3 m/s via Response Surface Method. The acquired rate of wear findings of the composites was examined for the utmost significant parameter, which was observed as sliding speed, followed by the load. The load factor was the solitary factor that had an impact in both the linear and square terms, whereas the weight fractions of the cenosphere and molybdenum disulphide had the minimum bearing effects. The wear percentage is primarily influenced by the combinative influence of the weight fraction of cenosphere – weight fraction of molybdenum disulphide, load – weight fraction of molybdenum disulphide, weight fraction of molybdenum disulphide – sliding speed and load – sliding speed. Despite their relatively small percentage contributions, cenosphere and MoS2 have been discovered to have a significant outcome on the wear rate of composite materials. The rate of wear also tends to decrease as cenosphere, and molybdenum disulphide weight percentages raise.
n
Keywords: HAMMCs, AA7075, Cenosphere, Molybdenum Disulphide, Wear Rate, Response Surface Methodology
n[if 424 equals=”Regular Issue”][This article belongs to Journal of Polymer and Composites(jopc)]
n
n
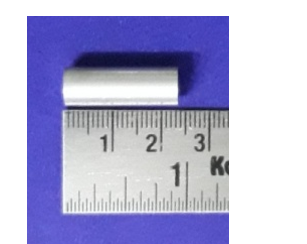
n
n
n
n
n[if 992 equals=”Open Access”] Full Text PDF Download[/if 992] nn
n[if 379 not_equal=””]nBrowse Figures
n
n
n[/if 379]n
References
n[if 1104 equals=””]n
- Evans, A., Marchi, C.S., Mortensen, A., Metal Matrix Composites in Industry: An Introduction and a Survey. Springer Science+Business Media, US; 2003.
- Ravi Kumar, D.V., Seenappa, Asha, P.B., Prakash Rao, C.R., Influence of Percent Filler on Tensile Strength, Impact Strength and Wear Properties of the Al7075-Cenosphere Composite. Materials Today: Proceedings, 2018, vol. 5, no. 5, p. 11697–11708, DOI: 1016/j.matpr.2018.02.139
- Kumarasamy, S.P., Vijayananth, K., Thankachan, T., Muthukutti, G.P., Investigations on mechanical and machinability behavior of aluminum/flyash cenosphere/Gr hybrid composites processed through compocasting. Journal of Applied Research and Technology, 2017, 15, no. 5, p. 430-441, DOI: 10.1016/j.jart.2017.05.005.
- Sharma, V.K., Singh, R.C., Chaudhary, R., Effect of flyash particles with aluminium melt on the wear of aluminium metal matrix composites. Engineering Science and Technology, an International Journal, 2017, vol. 20, no. 4, p. 1318–1323, DOI: 1016/j.jestch.2017.08.004.
- Saravanan, V., Thyla, P.R., Balakrishnan, S.R., Optimization of wear behavior on cenosphere-aluminium composite. Korean Journal of Materials Research, 2015, vol. 25, no. 7, p. 322-329, DOI: 10.3740/MRSK.2015.25.7.322.
- Raja Kumar, M., Shunmuga Priyana, M., Mani, A., Investigation of Mechanical and Wear properties of Aluminum-Fly Ash composite material produced by Stir Casting Method, International Journal of Scientific & Engineering Research, 2014, vol. 5, no. 5, p. 1261-1269.
- Reddy, B.R., Srinivas, C., Fabrication and Characterization of Silicon Carbide and Fly Ash Reinforced Aluminium Metal Matrix Hybrid Composites. Materials Today: Proceedings, 2018, vol. 5, no. 2, p. 8374-8381, DOI: 10.1016/j.matpr.2017.11.531.
- Kumar, V., Gupta, R.D., Batra, N.K., Comparison of Mechanical Properties and Effect of Sliding Velocity on Wear Properties of Al 6061, Mg 4%, Fly Ash and Al 6061, Mg 4%, Graphite 4%, Fly Ash Hybrid Metal Matrix Composite. Procedia Materials Science, 2014, vol. 6, p. 1365-1375, DOI: 10.1016/j.mspro.2014.07.116.
- Ekka, K.K., Chauhan, S.R., Varun, Effect of different reinforcements on sliding wear of aluminium matrix composites using Taguchi design of experimental technique. Indian Journal of Engineering and Materials Sciences, 2014, vol. 22, no. 2, p. 195-202.
- Ekka, K.K., Chauhan, S.R., Varun, Study on the effects of micro size ceramic particulates (SiC, Al2O3 and cenosphere) on mechanical, friction and sliding wear behaviour of aluminium matrix composites under dry sliding condition. Journal of Engineering Tribology, 2014, vol. 228, no. 6, p. 682-691, DOI: 10.1177/1350650114526581.
- Alidokht, S.A., Zadeh, A.A., Assadi, H., Effect of applied load on the dry sliding wear behaviour and the subsurface deformation on hybrid metal matrix composite. Wear, 2013, vol. 305, no. 1-2. p. 291-298, DOI: 10.1016/j.wear.2012.11.043.
- Patle, H., Mahendiran, P., Sunil, B.R., Dumpala, R., Hardness and sliding wear characteristics of AA7075-T6 surface composites reinforced with B4C and MoS2 Materials Research Express, 2019, vol. 6, no. 8, p. 1-12, DOI: 10.1088/2053-1591/ab1ff4.
- Vinoth, K.S., Subramanian, R., Dharmalingam, S., Anandavel, B., Mechanical and tribological characteristics of stir-cast Al-Si10Mg and self-lubricating Al-Si10Mg/MoS2 Materiali in Tehnologije, 2012, vol. 46, no. 5, p. 497-501.
- Ranjan, A., Shanmugasundaram, A., Experimental Investigation of Mechanical and Tribological Properties of Al 7075—MoS2/ZrO2/Ni Hybrid Composite. Advances in Materials and Metallurgy, 2019, p. 299-309, DOI: https://doi.org/10.1007/978-981-13-1780-4_29.
- Ansih, A., Kumar, M.A., Characterization of aluminium matrix reinforced with tungsten carbide and molybdenum disulphide hybrid composite. Materials Science and Engineering, 2018, vol. 402, no.1, p. 1-9, DOI: 10.1088/1757-899X/402/1/012006.
- Jojith, R., Radhika, N., Mechanical and tribological properties of LM13/TiO2/MoS2 hybrid metal matrix composite synthesized by stir casting. Particulate Science and Technology, 2019, vol. 37, no. 5, p. 566-578, DOI: 10.1080/02726351.2017.1407381.
- ASTM G99-05 – Standard Test Method for Wear Testing with a Pin-on-Disk Apparatus, ASTM International, West Conshohocken, 2010.
- Rebba, B., Ramanaiah, N., Evaluation of Mechanical Properties of Aluminum Alloy (Al-2024) Reinforced with Molybdenum Disulphide (MoS2) Metal Matrix Composites. Procedia Materials Science, 2014, vol. 6, p. 1161 – 1169, DOI: 10.1016/j.mspro.2014.07.189.
nn[/if 1104][if 1104 not_equal=””]n
- [foreach 1102]n t
- [if 1106 equals=””], [/if 1106][if 1106 not_equal=””],[/if 1106]
n[/foreach]
n[/if 1104]
nn
nn[if 1114 equals=”Yes”]n
n[/if 1114]
n
n
n
Volume | 11 | |
[if 424 equals=”Regular Issue”]Issue[/if 424][if 424 equals=”Special Issue”]Special Issue[/if 424] [if 424 equals=”Conference”][/if 424] | 13 | |
Received | October 28, 2023 | |
Accepted | December 21, 2023 | |
Published | February 15, 2024 |
n
n
n
n
n
nn function myFunction2() {n var x = document.getElementById(“browsefigure”);n if (x.style.display === “block”) {n x.style.display = “none”;n }n else { x.style.display = “Block”; }n }n document.querySelector(“.prevBtn”).addEventListener(“click”, () => {n changeSlides(-1);n });n document.querySelector(“.nextBtn”).addEventListener(“click”, () => {n changeSlides(1);n });n var slideIndex = 1;n showSlides(slideIndex);n function changeSlides(n) {n showSlides((slideIndex += n));n }n function currentSlide(n) {n showSlides((slideIndex = n));n }n function showSlides(n) {n var i;n var slides = document.getElementsByClassName(“Slide”);n var dots = document.getElementsByClassName(“Navdot”);n if (n > slides.length) { slideIndex = 1; }n if (n (item.style.display = “none”));n Array.from(dots).forEach(n item => (item.className = item.className.replace(” selected”, “”))n );n slides[slideIndex – 1].style.display = “block”;n dots[slideIndex – 1].className += ” selected”;n }n”}]